Table of Contents
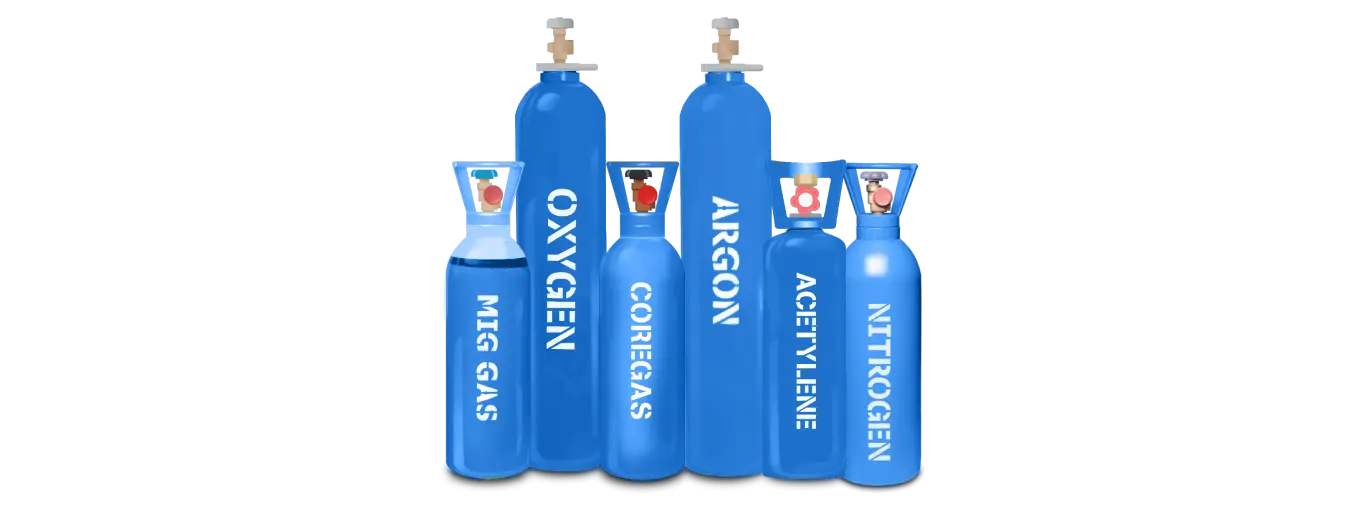
Every successful weld begins with choosing the right shielding gas. Whether you're working with stainless steel, carbon steel, or specialty alloys, your choice of shielding gas directly impacts weld strength, appearance, and overall quality. But managing your gas supply shouldn't be complicated. That's where Trade N Go Gas™ comes in.
These gases serve multiple functions during the welding process – they protect the molten metal from atmospheric contamination, influence the arc stability, affect penetration depth, and can even determine your welding speed. Through Proline Industrial, Coregas offers a comprehensive range of industrial gases and mixtures designed to optimize your welding performance, regardless of your application or industry.
Understanding Shielding Gases: The Foundation of Quality Welding
Before we explore how Trade N Go Gas™ can revolutionise your gas management, let's understand the crucial role of different welding gases:
Acetylene: The Versatile Powerhouse
- The hottest and most efficient fuel gas available
- Perfect for oxyacetylene cutting, welding, and flame heating
- Essential for flame hardening, straightening, and thermal spraying
- Ideal for underground use due to low ignition energy
Argon: The Clean Welder's Choice
- Available as compressed gas or cryogenic liquid (LAR)
- Ideal for TIG welding stainless steel and MIG/TIG welding of copper alloys
- Creates cleaner welds with fewer imperfections
- Essential for plasma cutting applications
CO2: The Cost-Effective Solution
- Perfect for MIG welding steel up to 10mm
- Ideal for carbon and alloy steel with flux-cored wire
- Versatile applications including plasma cutting and pipe freezing
- Cost-effective for thicker material applications
Coregas09: The Premium Blend
- 91% argon and 9% CO2 mixture
- Excellent for MIG welding carbon steel
- Produces clean, economical welds
- Ideal for robotic welding applications
Oxygen: The Essential Partner
- Critical for cutting, brazing, and soldering
- Achieves higher flame temperatures than air
- Improves arc stability and weld pool fluidity
- Available in compressed or liquid form (LOX)
Optimising Your Welding Process
The right gas mixture can significantly improve your welding outcomes:
- Enhanced metal transfer characteristics
- Better weld pool control
- Improved penetration depth
- Increased welding speed
- Reduced fume formation and spatter
- Better arc stability
Introducing Trade N Go Gas™: The Smart Way to Manage Your Gas Supply
Managing welding gases traditionally meant choosing between costly cylinder rentals or significant upfront purchases. Trade N Go Gas™ offers a better way:
How It Works?
The Trade N Go Gas™ system allows users to avoid ownership and long-term rental commitments. Instead, customers simply pay a one-time, refundable deposit for the cylinder and the gas cost, giving them complete control over how long they hold onto the cylinder. Once the gas has been used, the empty cylinder can be traded in at any participating stockist for a total replacement or returned for a complete refund of the deposit if no further gas is required.
- Pay a one-time, refundable deposit for your cylinder
- Purchase only the gas you need
- Exchange empty cylinders for full ones at any stockist
- Return cylinders for a full deposit refund when you're done
Key Benefits
1. Freedom from Contracts
- No long-term commitments
- Use gas as needed
- Return cylinders at any time
- Full deposit refund available
2. Cost Efficiency
- Pay only for the gas you use
- No ongoing rental fees
- Eliminate unused cylinder charges
- Perfect for fluctuating gas needs
3. Nationwide Accessibility
- Over 50 stockists across New Zealand
- Easy cylinder exchange
- Convenient locations
- Reduced downtime
4. Quality Assured
- European and US-sourced cylinders
- 100% asbestos-free acetylene cylinders
- Regular safety inspections
- Maintained to highest standards
5. Zero Maintenance Burden
- No cylinder maintenance required
- All safety checks handled by Coregas
- Compliance taken care of
- Focus on your core business
Perfect for all Operations
- Small workshops with occasional needs
- Large-scale production facilities
- Multi-site businesses
- Project-based operations
Advanced Welding Support
When you choose Trade N Go Gas™, you're not just getting gas supply - you're getting access to gases optimised for various welding techniques:
Short Arc Welding
- Ideal for thin plates
- Perfect for out-of-position welding
- Minimal spatter production
Spray Arc Welding
- High deposition rates
- Smooth welds
- Minimal spatter
- Ideal for thicker materials
Pulsed Arc Welding
- Versatile across power levels
- Excellent with argon-rich mixtures
- Superior control
A Sustainable Choice
Trade N Go Gas™ supports environmental responsibility:
- Reduced cylinder waste
- Efficient cylinder reuse
- Extended equipment lifecycle
- Minimised environmental impact
Take Control of Your Gas Supply Today
Selecting the right shielding gas is crucial for quality welding - but managing your gas supply shouldn't be a burden. Trade N Go Gas™ offers the perfect balance of flexibility, convenience, and cost-effectiveness.
Contact Proline Industrial today to discover how Trade N Go Gas™ can transform your welding gas management. With our extensive network of stockists and comprehensive range of high-quality gases, we're ready to support your welding success.