Table of Contents
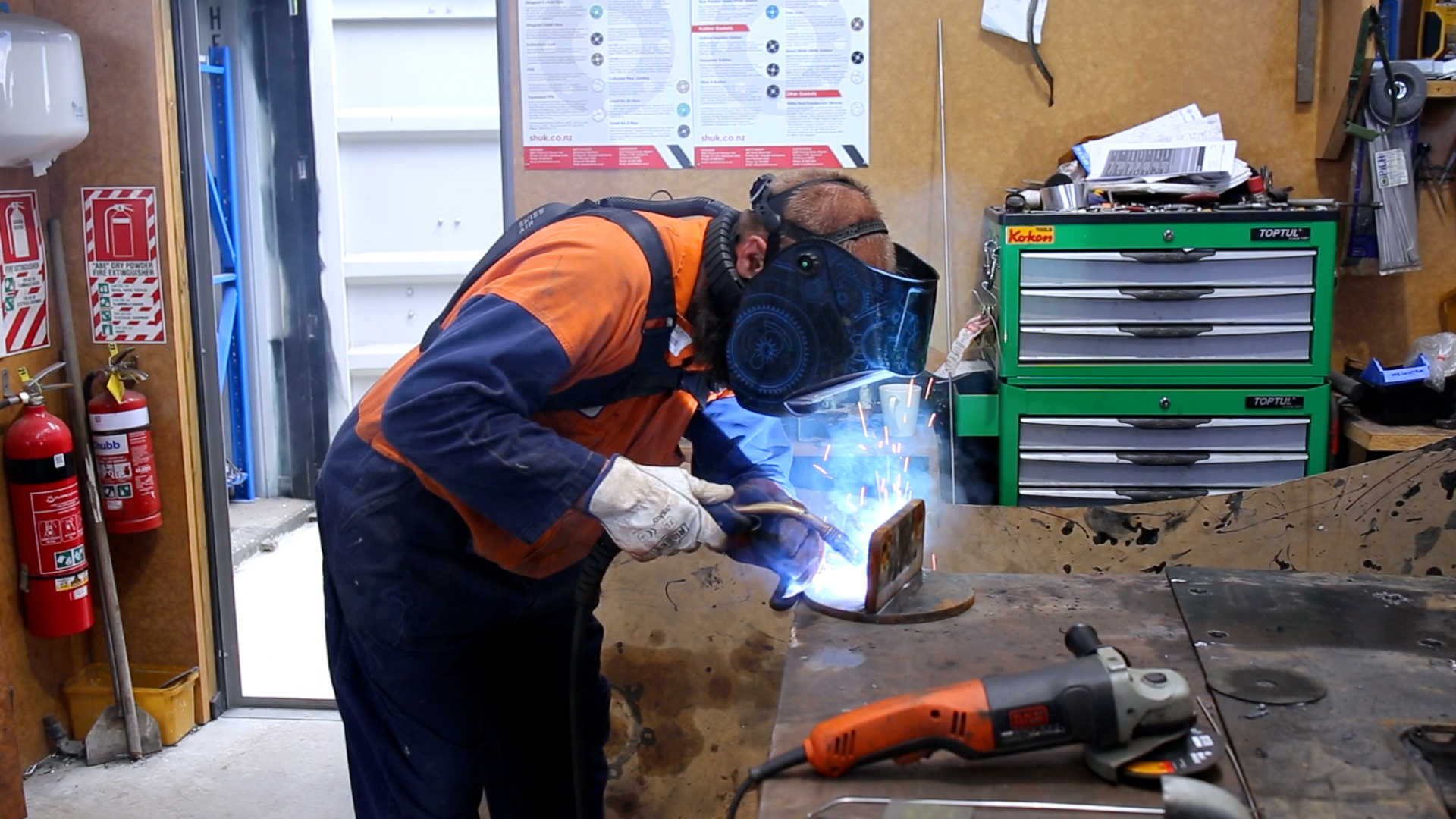
In the demanding engineering field, where welding and grinding are daily necessities, adequate respiratory protection cannot be overlooked. Paul Grayson of Smith Engineering shares invaluable insights into the advancements in respirator technology setting new standards in worker safety and comfort.
Navigating Confined Spaces with Respiratory Protection in Engineering Environments
Traditional respiratory protection often falls short in the unique conditions engineers like Grayson encounter. Bulky helmets and cumbersome systems, like Speedglas, hinder movement in confined spaces and fail to seal against harmful fumes, particularly for workers searching for beard-friendly options. In Grayson's words, “The respirator system is priceless when you're grinding the bottom of a rusty boat.” This firsthand experience shows the significance of reliable and adaptable respiratory protection, especially in environments saturated with welding fumes or when working in confined spaces like the undersides of vessels with corroded surfaces.
Enter the new era of Optrel respirator technology, demonstrated by the Optrel Swiss Air System. Grayson praises it for its extreme adaptability, weighing in at only 1200g – “This is a super light system; you just stick it on your head and carry on doing your job”. Unlike the heavy, obtrusive gear of the past, this offers a pressurised fit that is beard-friendly and prevents lens fogging, ensuring clear vision and clean air intake in all workshop and worksite situations.
Grayson confirms this when he comments, “This system fits around my beard better... and you don't get any fumes getting back in.” Its slim design and ease of use, with a simple fan flow adjustment and an extended battery life, allow workers to focus on their jobs without the constant distraction and discomfort of traditional masks.
Welding Safety Revolution: A Necessity, Not a Luxury
Grayson's comparative analysis reveals a stark contrast between his previous use of the Speedglas system and his current Optrel Swiss Air System, as he attests, “All the systems that I have used, this is by far the most comfortable and versatile system”. This personal testimony highlights the system's exceptional ability to safeguard against inhaling neighbouring fumes in the confined spaces of welding operations while providing an elevated level of protection and comfort without the bulk and discomfort associated with full helmets.
The most compelling aspect of Grayson’s interview is the emphasis on respiratory health through insights from seasoned welders, who reflect on their careers with a common regret: “The biggest regret is not taking enough care of their lungs.” Grayson echoes this sentiment, emphasising the minimal cost of the Optrel Swiss Air System compared to the priceless benefit of preserved lung health over decades. This resonates deeply within a profession where the long-term implications of inhaling harmful fumes have only recently been fully acknowledged.
Through his narrative, Grayson champions the new respirator system not just as a tool but, more importantly, as a critical investment in the health and productivity of workers in the industrial sector. With its superior filtration and pressurised design, it presents a solution that could mitigate these risks, offering a layer of safety that is becoming increasingly important. His recommendation is clear: adopting this technology is not just a matter of convenience but necessity, “just do it, you won’t regret it.”
In conclusion, the advancements in respiratory protection technology represent a significant leap forward in safeguarding the health of those in the engineering and broader industrial fields. Paul Grayson's advocacy for the Optrel Swiss Air System serves as a compelling call to action for welders, engineers, and workshop owners alike to re-evaluate their safety equipment and commit to the well-being of their employees. In the words of Grayson, embracing this latest respiratory technology is a decision that no one will regret; it is not just an investment in equipment but in the future of the workforce itself.
Watch the interview here: