Table of Contents
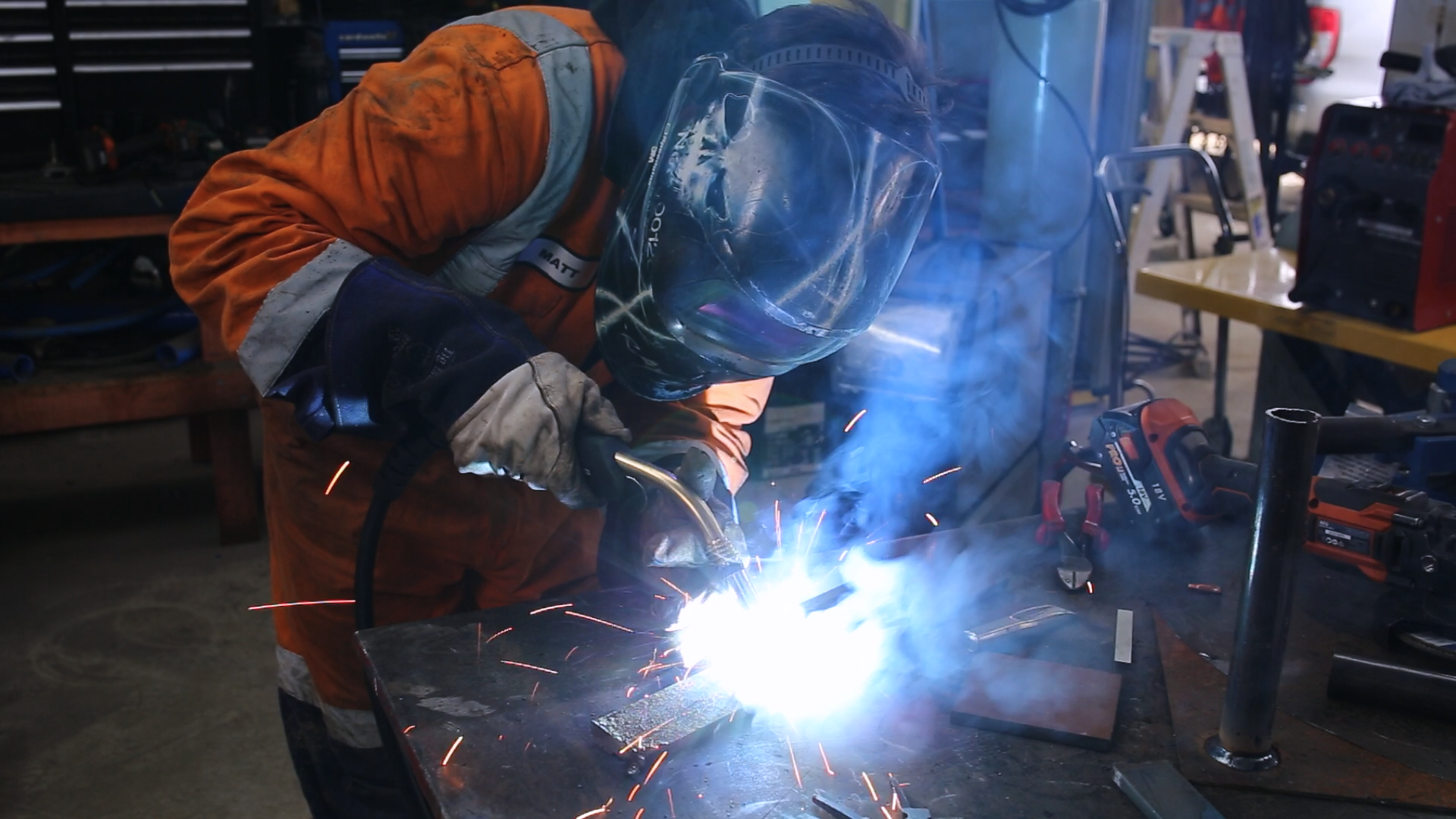
Selecting the right generator for your inverter welder is essential as it significantly influences operational efficiency and equipment safety. While mains power usually provides a stable energy source, field and remote operations often depend on generators. However, generators can vary significantly in power quality. This article explores the importance of choosing the right generator for your inverter welder and offers insights on selecting and utilising it to maximise efficiency and safety.
Understanding Generator Power
Unlike mains power, which is typically stable and reliable, generator power can be inconsistent. Often termed 'dirty' power, this inconsistency can severely damage sensitive electronic components within inverter welders. These fluctuations are notably pronounced in portable generators, which, despite their affordability and mobility, may not be suitable for powering sensitive devices due to the quality of power they produce. The electrical output from some generators, especially those not designed for electronic equipment, includes voltage fluctuations that can degrade sensitive components over time.
The Risks of 'Dirty Power'
'Dirty power’ refers to electrical supply irregularities or voltage and current output noise. A stable power supply is essential for inverter welders, which use sophisticated electronic controls to convert AC to DC. An inverter welder takes standard 60Hz AC power and runs it through an initial rectifier, turning it into high-voltage DC power. A microprocessor using extremely high-speed transistor switching turns the DC power off and on again at a very high rate (in Miller welders, for example, 60,000 times a second), which then simulates the waveform of AC power, but at 1,000 times the frequency. That high-frequency AC power then passes through a transformer to another rectifier that converts the power back to DC on its way to the tip of the welding wire. An unstable power supply can disrupt the welding process, reduce weld quality, and damage the welder's internal circuitry, potentially leading to costly repairs or replacements.
Voltage fluctuations can be sudden spikes or troughs, harmful over short and long periods. Sudden spikes can overload and burn out electronic components, while prolonged low voltages can cause ineffective welding performance and increased wear and tear on the welder’s internal components. To manage these risks, it's crucial to understand how to choose a generator that provides as clean and stable a power output as possible.
Reasons Why Voltage Surges and Spikes Occur
- Generator Quality: All portable generators produce power that may not be as consistent as perfect sine wave power. This variation is quantified as 'Total Harmonic Distortion' (THD). Generally, a 6% or less THD rating is acceptable for a portable generator. However, the market has recently seen an influx of inexpensive, low-quality generators with THD ratings exceeding 6%. Although these generators might handle essential power tools adequately, they are not suitable for powering devices like inverters that require stable voltage, as they are prone to severe voltage fluctuations and spikes.
- Start Up and Shut Down: During the start-up and shut-down phases, the generator's engine does not operate smoothly or at a constant speed, which can cause the power output to fluctuate in line with changes in engine speed.
- Fuel Supply Interruption: Similar to the start-up and shut-down scenarios, interruptions in fuel supply can cause the engine to vary its speed unpredictably. This often results in the generator producing power fluctuating significantly, which can be problematic for connected devices.
- Loading vs. Generator Size: A generator that is either too small for the demand or overloaded will struggle to maintain a steady current supply. When the load is suddenly removed, such as when stopping welding activities, the engine may over-rev until it stabilises at an idle speed. This over-revving can lead to dangerously high increases in voltage output.
- Additional Loads: Operating additional heavy-load devices, such as grinders or cut-off saws, on the same generator used for a welding machine can lead to overloading. If the generator's capacity is insufficient to handle all devices at once, this can cause further fluctuations in the power output.
- Lack of Maintenance: A generator that is not regularly maintained may perform as poorly as a low-quality generator. Such neglect can lead to inconsistent power delivery, mirroring the problems seen in cheaper models.
Protecting Inverter Welders
Inverter welders are particularly vulnerable to power fluctuations due to their reliance on components like capacitors and Insulated-Gate Bipolar Transistors (IGBT). These parts are susceptible to damage from the irregular power supplied by low-quality generators. Manufacturers have addressed these risks by incorporating technologies such as Voltage Sensing Devices and High Voltage Capacitors, which help mitigate the risks associated with voltage fluctuations. For example, Voltage Sensing Devices monitor the input voltage and can shut off power to sensitive components if abnormal voltages are detected.
Our Recommendations
At Proline Industrial, we understand that many operators, particularly in the rural, construction, and maintenance sectors, often rely on generators to power their welding equipment. Proline Industrial machines are designed to be less susceptible to damage from power irregularities thanks to rigorously tested components and certified to handle generator-induced fluctuations. Some of these design features include:
Generator Compatibility: Specifically engineered to perform reliably when powered by generators.
Voltage Tolerance: Incorporates technology capable of handling a range of input voltages, minimising the impact of fluctuations.
Integrated Power Stabilisation: Features built-in systems that stabilise power supply, ensuring consistent performance.
Robust Internal Components: Uses high-quality components to withstand variable power conditions.
Advanced Inverter Technology: Employs modern inverter technology that efficiently manages power use and maintains stable output.
The Strata AdvanceMig255C is an exceptional choice for anyone needing a generator-compatible welder. With its specialised design that embraces generator use, this welder guarantees performance stability even under challenging power conditions. Its advanced inverter technology and robust internal components are tailored to mitigate power supply fluctuations, making it an ideal machine for remote, rural, or on-the-go welding needs. The Strata AdvanceMig255C meets the demands of various industries and provides the reliability and peace of mind needed when working away from conventional power sources. This makes it a highly recommended choice for professionals who require dependable welding machines while working out in the field.
Guidelines for Generator Use
Choosing the right generator involves more than just assessing its size and power output; quality and compatibility with the welder are crucial considerations. It is advised to select generators with a Total Harmonic Distortion (THD) of less than 6% to ensure minimal risk to the welder. Additionally, maintaining generators in good working condition and ensuring they are neither under-sized nor over-loaded is vital to prevent power output fluctuations.
In the next part of this blog post, we will discuss practical tips for generator purchase and provide a comprehensive guide to selecting a generator that meets the needs of your welding operations, ensuring longevity and efficiency.
Practical Tips for Generator Purchase
When purchasing a generator for an inverter welder, it's essential to consider more than just the wattage. The generator's THD (Total Harmonic Distortion) rating, build quality, and ability to provide a consistent power output without surges are paramount. These factors play a crucial role in determining whether a generator can reliably power a welder without risking damage to its sensitive electronic components.
A generator with a low THD rating, typically less than 6%, ensures the power output is clean and stable, mimicking mains power as closely as possible. This is critical for safely operating inverter welders within strict voltage tolerances. Additionally, high-quality generators will have robust build quality and reliable voltage regulation mechanisms that protect against power fluctuations.
Another essential factor is the welder's amperage and power requirements to ensure a generator is compatible with your specific inverter welder. Manufacturers often provide guidelines on their machines' minimum and ideal generator sizes. For instance, a welder that operates at 200 amps might require a generator with a minimum output of 8 kVA. In contrast, a ten kVA generator could be ideal for additional capacity and ensure smooth operation even under load.
It's also essential to consider the simultaneous use of other equipment. Suppose a generator powers the welder and other grinders or drills. In that case, it should have enough capacity to handle the combined load without straining. This ensures that the generator can maintain a stable output, preventing voltage drops that could affect the welder’s performance.
Suggested minimum generator size guide table
Inverter Machine Type | Max. Output | Suggested "Minimum" Generator Size2 | Suggested "Ideal" Generator Size3 |
Welder | Up to 130A | 6 kva(5 kw4) | 7 + kva(5 kw4) |
140 - 160A | 7 kva(5.5 kw4) | 8 + kva(6.5 kw4) | |
180 - 200A | 8 kva(6.5 kw4) | 10 + kva(8 kw4) | |
250A | 13 kva(10.5 kw4) | 15 + kva(12 kw4) | |
300A | 15 kva(12 kw4) | 20 + kva(16 kw4) | |
350A | 25 kva(20 kw4) | 30 + kva(24 kw4) | |
400A | 35 kva(28 kw4) | 40 kva(32 kw4) | |
Plasma Cutter | 30A | 7 kva(5.5 kw4) | 8 + kva(6.5 kw4) |
40 - 45A | 8 kva(6.5 kw4) | 10 + kva(8 kw4) |
1. Note that if it is intended that the generator will be used to run additional equipment at the same time as the welder, the generator size should be increased accordingly. These figures are an approximate guide only and should not replace the manufacturer's recommendations.
2. 'Minimum'' size is the smallest that we suggest to minimise the risk of voltage spikes, etc, however it may not be enough to achieve full output from the welder.
3. 'Ideal' size will further minimise risk of power supply issues and will allow a higher output from the welder.
4. Approximate equivalent kw size of inverter generators, based on generator power factor of 0.8. This may vary if the generator used has a different power factor check with the generator manufacturer.
Generator Operation & Maintenance Tips
Before starting or stopping your generator, always disconnect the welder’s power lead to avoid any power surges that could damage the equipment. Additionally, ensure the generator has a reliable fuel supply, and the fuel line is in good condition, preventing the engine from running out of fuel while connected to the welder. Regular generator maintenance cannot be overlooked; a generator needing service or replacement should not be used. Lastly, the quality of power extension leads matters significantly. Avoid using worn-out or low-quality leads; instead, opt for heavy-duty leads as recommended in the guidelines. These steps are crucial for maintaining the safety and functionality of your welding setup.
Table: Guide for cable size of extension leads used with Inverter Welders Table
Welding Machine Max. Output | Power Supply | Suggested Minimum Cable Size* |
UP to 200A | 240V 10A/15A | Lengths up to 10m: 2.0mm2 Lengths up to 10m: 2.5mm2 |
250A | 240V 15A | 2.5mm2 |
240V 20/25/32A | 4.0mm2 |
*These figures are an approximate guide only and should not replace manufacturers' recommendations.
Regular maintenance is critical to the longevity and reliability of any generator. Routine checks and servicing can prevent many common problems associated with generator use, such as fuel issues, oil levels, and filter changes. Ensuring the generator is serviced according to the manufacturer’s guidelines will help maintain its efficiency and output stability.
Using Liquid Engineering Fuel Set can significantly enhance the longevity and performance of fuel stored in generators. This high-quality fuel stabiliser and conditioner ensures your fuel system remains clean, maintaining engine performance and fuel economy. Fuel Set is effective for diesel and petrol engines, making it versatile for various generator types.
One of the primary benefits of using Fuel Set is its ability to rejuvenate stale fuel, making it viable again for use. This is particularly useful for generators that may not be used regularly and where fuel can sit idle for extended periods. Additionally, Fuel Set removes water from the fuel lines and dissolves deposits such as wax, gum, and varnish that can build up in the fuel system and injectors. It also tackles issues like diesel bug and fungal growth, which can severely impact fuel quality and engine health. By reducing emissions and preventing corrosion within the fuel system, Fuel Set extends the life of the fuel and the generator itself. Available in a range of sizes from 200ml to 20L, it offers a practical solution for different needs, ensuring that your generator is always ready with reliable and efficient fuel.
Proper generator storage is also essential, particularly in environments prone to dust, moisture, or extreme temperatures, affecting its performance. A well-maintained generator will provide reliable service for many years, making it a worthwhile investment for any professional welder.
Proline Industrial Inverter Compatible Generator Recommendation
For construction and rural engineers seeking a reliable and robust generator, the GT Power GT10000ESQ is an exceptional choice. This powerhouse generator can run demanding tools and equipment thanks to its high output and strong engine. Still, its advanced features, like the Tomahawk Alternator and AVR, ensure it can safely power inverter-based technologies. The GT10000ESQ’s large fuel capacity and extended runtime make it ideally suited for long days on the job site or in remote locations, ensuring you have the power you need whenever and wherever you need it. Its power, versatility, and reliability make the GT10000ESQ an excellent option for professionals in demanding fields.
Design features that ensure it is inverter welder compatible:
Robust Power Output: The GT10000ESQ features a maximum output of 9000W, which is ideal for demanding applications such as powering welding machines up to 200A.
Advanced Technology: Equipped with the patented Tomahawk Alternator and Automatic Voltage Regulator (AVR), it ensures stable and consistent power delivery suitable for sensitive electronics and inverter-based devices.
Durable Engine Design: Powered by a 16HP Powerdyne 4-stroke OHV engine, this generator is built for professional and industrial use.
Extended Operation: A 25L fuel tank provides up to 8 hours of runtime at 50% load, making it suitable for prolonged use without frequent refuelling.
Safety Features: Includes a low oil alert with automatic shutdown to protect the engine from damage due to low oil levels.
Watch the GT Power GT10000ESQ in action with the Strata AdvanceMig255C HERE.
When assessing potential purchases, requesting detailed specifications and possibly a demonstration to see the generator in action is advisable. Checking customer reviews and seeking recommendations from experienced users can also provide valuable insights into the generator's performance and reliability under real-world conditions. Additionally, viewing demonstrations and reviews on the Proline Industrial YouTube channel can offer further clarity and help make an informed decision.
In conclusion, integrating a suitable generator with an inverter welder can significantly enhance performance and longevity. By understanding the technical requirements and potential risks associated with powering welders through generators, operators can make informed decisions that ensure safety, efficiency, and productivity. We encourage you to prioritise quality and suitability over cost when selecting a generator for your welding operations, ensuring your equipment operates efficiently without risk of damage. If you’re ready to enhance your welding operations, contact our team at Proline Industrial today to find the perfect generator for your inverter welder.